Do you get a lot of feedback about damaged or defective items? Or do your customers complain about the wrong product description?
If that’s the case, it’s time to reevaluate your product development process and take better steps to ensure your products never get returned again. In fact, product returns usually indicate that there’s a more significant issue to keep an eye on — a drop in quality. While it’s only normal for errors to happen, you should do everything you can to prevent such errors from happening in the first place.
How exactly should you do that? Well, it all boils down to quality — the cost of quality — to be precise.
In this blog post, we’ll explain what the cost of quality in project management is and dwell on the advantages and disadvantages of implementing it in your projects. We’ll also look into the costs associated with good and poor quality, and how project managers calculate the cost of quality.
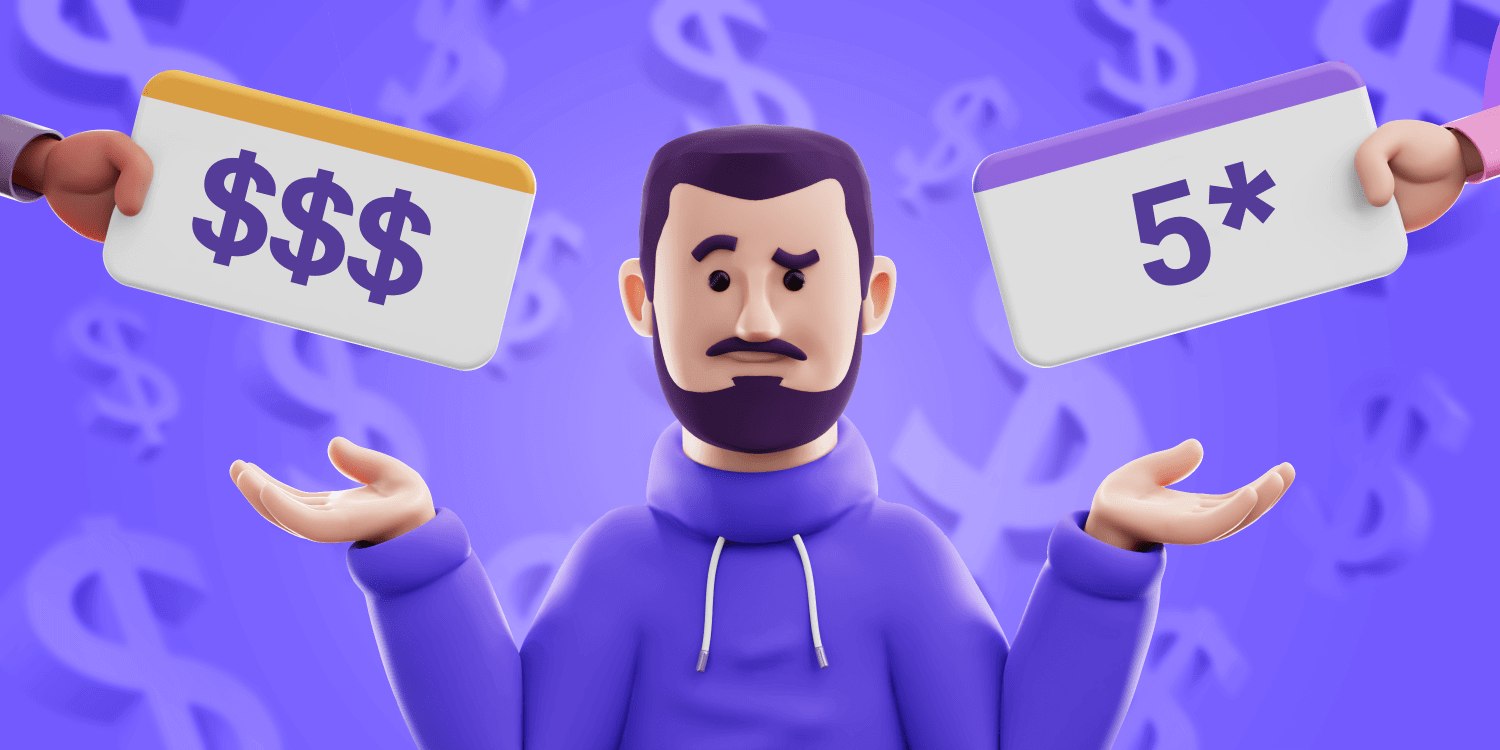
Table of Contents
What is cost of quality in project management?
According to the PMBOK guide: “Cost of quality (COQ) refers to the total cost of all efforts related to quality throughout the product’s life cycle.”
Some project areas might not have been done in accordance with the original plan, so the cost of quality may be incurred throughout the product’s life cycle. In other words, weak project management decisions can lead to several business-related consequences, including a drop in quality (or poor quality).
As a result, products get returned, customers claim the product warranty, or certain products get recalled from the end consumer (due to repair, substitution, or replacement).
Therefore, it’s the responsibility of the project manager to ensure that the product or service is fit for its purpose.
We spoke with Andrew Kovalev, an Official Member at Forbes Business Council, whose core expertise is restructuring and organizational strategic repositioning. Here’s what he says about the importance of paying attention to the cost of quality:
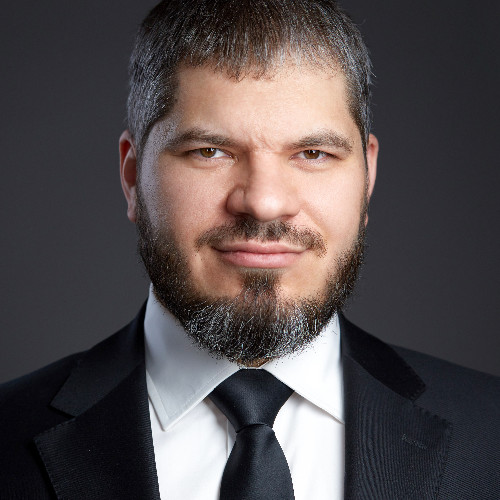
“Cost of quality management is not a one-time cost, it’s an ongoing and continuous process. Organizations should continuously monitor and measure the cost of quality to ensure that they are taking the appropriate steps to prevent defects and deal with defects that do occur.”
We were curious to learn what these defects encompass:
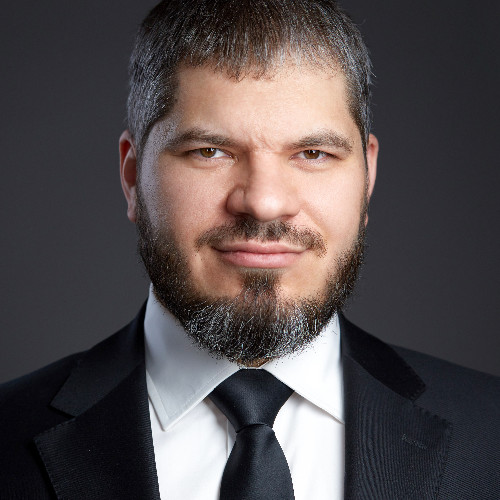
“This includes regularly reviewing and updating processes and procedures, as well as training employees on quality management techniques. Additionally, organizations should continuously monitor customer feedback and complaints to identify potential areas for improvement in terms of quality.”
If you’re just waiting until after production to identify and address quality defects in your products, you’re more likely to see a rise in the number of quality issues. By taking just a few preventative steps before production, you can limit the risk of quality lapse and reduce quality costs in general.
💡 Clockify Pro Tip
Read our blog post to learn how to control and analyze the costs associated with your project.
What are the types of cost of quality?
The cost of quality is the sum of two factors:
- The cost of conformance (cost of good quality or COGQ), and
- The cost of nonconformance (cost of poor quality or COPQ).
In other words, the cost of quality is the connection between the costs of establishing a quality product/service and the costs of establishing a poor quality product/service.
The cost of good quality (or the cost of conformance) comprises:
- Preventive, and
- Appraisal costs.
On the other hand, the cost of poor quality (the cost of nonconformance) deals with:
- Internal, and
- External failure costs.
Quality costs, however, are not specific to manufacturing only, but rather they remain relevant from the beginning of research and development of the project to the point of interacting with customers.
The following four categories apply to the cost of quality model in general. Let’s go over each of the costs we’ve mentioned to see what business activities influence the quality of a product or service.
Type #1: Cost of conformance
Also called the cost of good quality (COGQ), the cost of conformance refers to the costs of activities that ensure the product or service meets the desired level of quality before it reaches the end consumer.
As we already mentioned, the cost of good quality consists of 2 more categories, such as:
- Preventive costs, and
- Appraisal costs.
Subtype #1: Preventive costs
Preventive costs arise from activities aimed at eliminating defects (nonconformities) from occurring in the first place.
According to the PMBOK guide, these include, but are not limited to the costs of:
- Adequate employee training. Proper training ensures project success because employees will be more effective in leading and implementing those projects.
- Quality planning. The process of identifying the most important aspects of the project during the planning stage to ensure that the initial plan is being followed.
- New product development process. The act of analyzing a product concept, features, or functionalities to understand how potential customers may use it.
- Launch of product specifications and standards. The process of outlining the specific features, functionalities, and technical standards needed to build the product.
- Process control. The process of planning, tracking, and managing all phases of the project lifecycle.
- Quality audit. The process of ensuring that project activities comply with the level of conformance to project requirements in order to prevent any deficiencies.
- Introducing a Quality Management System (QMS). A QMS will make it easier to record the necessary processes and procedures to meet quality objectives.
Other examples of prevention costs included in the PMBOK guide are:
- Time to do it right (Do it right attitude). This philosophy refers to delivering the right product to the right place at the right time. It is also about focusing the right level of energy on the right activities at the right time.
- Document processes. The costs related to the act of recording and documenting all the steps and tasks involved in developing a particular project from start to finish.
- Equipment. Costs related to the acquisition of the equipment, including sales tax, freight and handling fees, insurance while in transit, installation and assembly, and testing equipment performance.
Subtype #2: Appraisal costs
Appraisal costs are related to inspecting and testing products to ensure they meet quality standards and performance requirements after the product has been produced.
These include costs related to activities such as:
- Destructive testing loss. The method of testing the performance or material behavior of a product in order to check its durability (e.g., crash tests).
- Calibration of test equipment. The process of measuring and configuring instrument or machine parameters to ensure they remain within the predetermined limits.
- Supplier assessments. The process of evaluating potential and existing suppliers to ensure that the organization’s needs are met in terms of performance.
- Incoming material inspections. The procedure of validating the quality of raw materials and their components in order to prevent potential issues before pre-production.
- Inspections of received goods. Purchased goods must be inspected for quantity and quality to mitigate potential damages and ensure that they comply with specifications.
- In-process inspection and test. This refers to all inspections made at any stage of product production to check whether certain parameters follow the industry standards.
- Inspection of finished goods. The process of examining and testing the specifications and dimensions of a product when it’s ready for shipping or is at least 80% completed.
In sum, prevention and appraisal costs (cost of conformance) refer to the amount of money invested during the project to prevent project failures.
Type #2: Cost of nonconformance
Also called the cost of poor quality (COPQ), the cost of nonconformance refers to the costs of activities necessary to correct defects that have occurred despite a company’s efforts to avoid them.
These costs usually result from product defects, i.e., when a product doesn’t follow the necessary standards it was designed and manufactured to comply with.
The cost of nonconformance (or failure costs) are sub-categorized as:
- Internal failure costs (found by the project manager), and
- External failure costs (found by the customer).
Let’s see what each type refers to.
Subtype #1: Internal failure costs
Internal failure costs are related to rectifying all the nonconformities (defects) by the organization itself before the product or service has reached the end customer (the costs prior to delivery or shipment).
These include:
- Waste. Unnecessary work which results from poor documentation of the standards, insufficient quality controls, a lack of a defined process, inadequate product configuration, or undocumented design changes.
- Excessive scrap. Cost arising from unusable material (left after the product has been manufactured) due to issues such as product defects, material shortages, excessive downtime with equipment, and product redesigns.
- Rework or rectification of defective products. Costs related to the process of identifying and rejecting a certain product during production in order to correct defective, nonconforming materials.
- Machine breakdown. Improper maintenance leads to downtime incidents resulting in a myriad of costs, including lost profit, equipment repair, and equipment downtime.
Subtype #2: External failure costs
External failure costs are associated with revising all the nonconformities (defects) that are identified once the product has been delivered to the end customer.
These include:
- Liability lawsuits. Expenses or damage awards that result from product liability litigation due to quality issues related to the way the product was manufactured or a company’s violations of civil law.
- Service and repairs. Costs related to servicing the product (repairing, replacing, or adjusting components of both returned products and those on the market).
- Warranty claims. Costs associated with administering accepted claims (when a customer requests free repair or replacement of a product during the warranty period).
- Customer complaints. When a product doesn’t meet customer expectations in terms of quality, they will point out problems or defects which need to be addressed in order to improve their experience.
- Returns of products or materials. The costs of processing returned goods are usually high and result from various reasons, including unmet expectations, damaged or defective goods, buyer’s remorse, wrong product description, or incorrect fit.
Other examples of external failure costs found in the PMBOK guide are:
- Wrong sales orders. Order errors can be costly, regardless of whether they’re caused by an inadequate price, an incorrect item or part code, missing customer information, or a data entry error.
- Lost revenue. If a company delivers poor quality products, customers will not buy from them again. This counts as lost business deals (lost sales), as customers will most likely buy from someone else instead.
- Shipping damages. The cost of replacing damaged products is significant, yet an inevitable part of any organization. Damages usually result from inadequate packaging, improper handling, or water exposure.
In a nutshell, internal and external failure costs refer to the amount of money invested during an ongoing project or after the project’s completion due to failures.
What are the benefits of the cost of quality model?
Maintaining good quality is very important in relation to costs, but also offers a range of other benefits for organizations.
To learn more about such advantages, we contacted David O’Brien, a sole contributor to TheProjectManagement.Expert, and a certified Project Manager with 25+ years of experience in various project management methodologies. Here’s why David claims that managers should pay close attention to cost of quality:
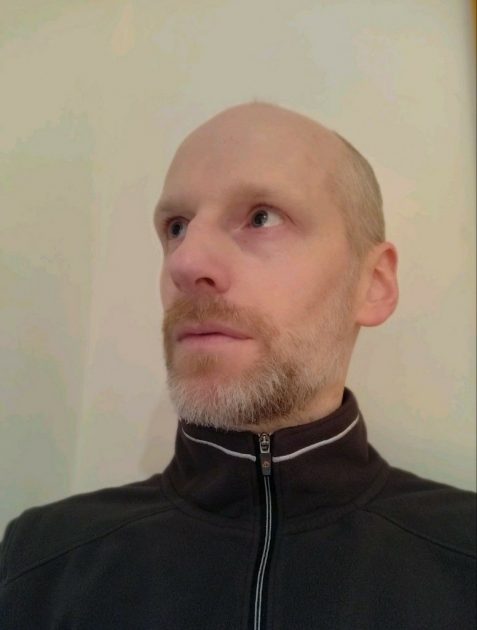
“It is the central consideration of any project deliverables — it is the balance between how many people should work on a project, how long the project should take and how much money is spent on the project.”
With that in line, implementing the cost of quality model will help you:
- Find a balance between the costs of quality, the project’s timeline, and the total budget,
- Spot problem areas in which the product quality could be improved,
- Examine the real reasons behind product nonconformance,
- Minimize failure and appraisal costs,
- Deliver the project on time and within budget,
- Prevent potential product defects, and
- Boost sales and profits.
As you can see from the above points, some of the key benefits of using the COQ model include:
- Improved decision making,
- Improved communication,
- Improved supplier management,
- Improved customer satisfaction and loyalty,
- Increased efficiency and productivity,
- Reduced costs, and most importantly,
- Improved quality.
Therefore, organizations that pay enough attention to the quality-related costs can further invest in areas that will have the biggest impact on raising project quality.
💡 Clockify Pro Tip
When you track a project properly, you can easily spot deviations from the intended plan.
What are the drawbacks of the cost of quality model?
Even though the cost of quality model comes with a great deal of benefits, there are still some potential drawbacks, which include:
- The potential for increased costs due to over-investing in quality assurance,
- The potential for decreased efficiency due to too much focus on quality assurance,
- An over-emphasis on managing costs rather than improving quality,
- Difficulty in accurately allocating costs to certain activities or areas of the project, and
- High upfront costs of tools and training can result in project failure if the projected sales do not materialize.
One additional drawback you might encounter if you decide to rely on the cost of quality model refers to the challenges of accurately measuring all the costs related to ensuring product quality.
However, relying on project accounting might help you record all the costs associated with a specific project. For example, you can combine several metrics (assuming that they constitute the total cost of quality), such as:
- The number of defects,
- The cost of inspections or testing, and
- The cost of repairs or corrections.
By combining the equations of all expenses associated with the above quality metrics, the total cost of quality can be more accurately calculated.
Grouping quality costs into separate categories can also help project managers make effective business decisions. Information about such costs should be reported in the existing accounting records of the company, as well as:
- Timesheets,
- Expense reports,
- Purchase orders, or
- Rework reports.
By looking at this information, project managers estimate quality costs more accurately.
How do you calculate the cost of quality?
Calculating the cost of quality is pretty straightforward because project managers use a predetermined formula to obtain the total cost.
There are two main components for calculating the total cost of quality:
- COGQ = Cost of good quality, and
- COPQ = Cost of poor quality.
Here’s how the formula goes:
Cost of Quality (COQ) = Cost of Conformance (COGQ) + Cost of Nonconformance (COPQ)
Perhaps the cost of quality formula seems simple. However, once you start digging deeper into the associated costs, it can get more complicated. Therefore, you need to be familiar with all the elements included in both conformance and nonconformance costs.
Let’s take a look at a breakdown of the above formula:
COQ = PC + AC + IFC + EFC
The elements from the formula refer to:
- PC = Prevention costs,
- AC = Appraisal costs,
- IFC = Internal failure costs, and
- EFC = External failure costs.
As you can see, project managers measure the cost of quality by adding up the costs associated with prevention, appraisal, and failure (e.g., costs associated with training, inspection, rework, scrap, etc.)
Cost of quality examples
As we already mentioned, measuring the cost of quality is necessary to maintain the overall quality of your products and services, and thus gain a competitive advantage. Here’s a step-by-step breakdown of the process for calculating the cost of quality.
Step #1: Calculate the total cost of conformance
The total cost of good quality can be calculated by summing up the costs of preventive and appraisal costs, which include:
- Employee training,
- Quality audit,
- Materials inspection, and
- Destructive testing loss.
Here’s a breakdown of preventive and appraisal costs:
COGQ = 17,700 + 45,200 + 8500 +19,000= 90,400
Step #2: Calculate the total cost of nonconformance
The costs that account for the total cost of poor quality are the costs of:
- Scrap,
- Rework,
- Warranty claims,
- Service, and
- Repairs.
These costs can be calculated like this:
COPQ= 14,600 + 9,700 +18,300 + 6,900 = 49,500
Step #3: Calculate the total COQ
Once you’ve finished calculating the cost of good and cost of poor quality, here’s how the total cost of quality for a smartphone would look like.
Total COQ = Total COGQ + Total COPQ
90,400 + 49,500 = 139,900
We created this example to help you understand which costs you need to consider when calculating the cost of quality. In the table below, we included the overview of all costs.
Cost of Quality for a smartphone | |
---|---|
Cost of Conformance (COGQ) | Amount |
Prevention costs | |
Employee training | $17,700 |
Quality audit | $45,200 |
Appraisal costs | |
Destructive testing loss | $8,500 |
Materials inspection | $19,000 |
Cost of Nonconformance (COPQ) | |
Internal failure costs | |
Scrap | $14,600 |
Rework | $9,700 |
External failure costs | |
Warranty replacements | $18,300 |
Service and repairs | $6,900 |
Total Cost of Quality | $139,900 |
Keep track of project expenses in Clockify
As a project manager, you need to make informed decisions about how much to invest in quality. Apart from calculating the cost of quality manually, another way to do so is to use expense tracking software.
Clockify, for example, lets you record project-related expenses, and even track your project’s budget. That way, you can monitor your income and expenses, and understand how your project is performing financially. It also helps you reduce the cost of quality because it helps you stay on top of all the quality-related costs.
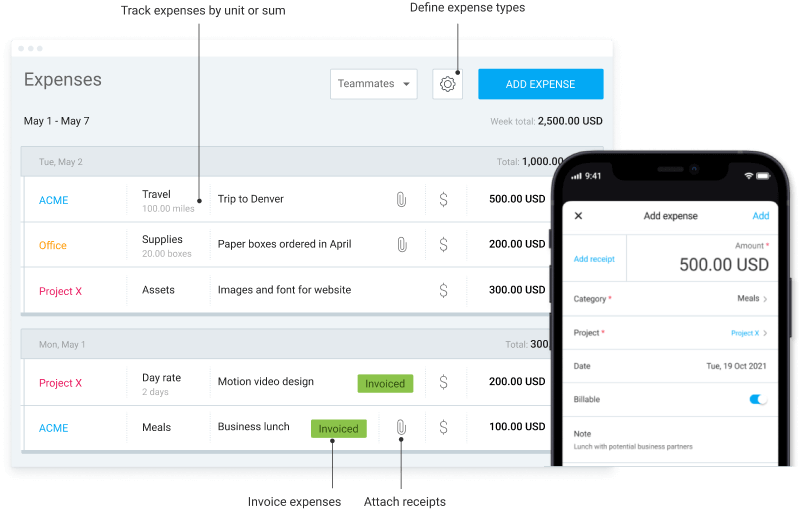
In addition to tracking your expenses, and creating an estimated project’s budget, Clockify can store important information about your company’s projects and allows you to generate project-related reports. That way, you are always aware of your project’s progress, and can identify whether operations are being carried out according to the pre-established documentation and plan. As a result, you can make precise project profitability estimates.
Moreover, if you’d like to track expenses in Clockify, but you also need a dedicated project management app and a team chat app altogether — check out the newest bundle plan, offering Clockify with 2 such apps at a special price.
Final words: Measuring the cost of quality will help you make informed project decisions
The cost of quality model helps companies reduce their costs by nudging them to identify and eliminate wasteful costs related to substandard quality.
This way, you can minimize the need for rework, warranties, and other nonconformance costs by focusing on preventative and assessment costs. Over the course of a project, paying attention to the cost of quality can contribute to:
- Significant cost savings,
- Greater client satisfaction, and
- Higher project profitability.
Additionally, if they give enough attention to measuring the cost of quality, companies can make better judgments about how to spend resources to achieve the desired quality level while keeping down the total quality costs.